Project Two.
£2,000 (ex VAT)
Ford Grille.
Overview: A custom vehicle provider wanted to produce a bespoke grille for the Ford Raptor and Ford Wildtrak trucks. This involved laser scanning the existing grille and parametrically reverse engineering the existing form before finally adding the additional modifications. The grille was then manufactured using reaction injection moulding.
-
We ideally need to scan the part in a single set-up with thinned wall parts such as this grille. If we were to scan the front face and then flip the part to scan the rear, the part would likely deform, and the two scans would not accurately come together.
-
Reverse engineering automotive components are never without complications due to the organic flowing surfaces that need to tie in with the rest of the vehicle.
-
The inspection process for this part was relatively simple as we had made significant modifications to the part. Our primary inspection was to ensure that the external shape accurately matched the existing scan data to guarantee an accurate gap and flush.
-
We will not cover the manufacturing costs in this overview as there are many variables to consider for manufacturing. However, we used reaction injection moulding to produce a batch of x10 grilles. Reaction injection moulding uses a 3D printed master mould to create a silicon tool suitable for injection moulding. For a part such as this, you will be able to manufacture x50 units from a single tool.
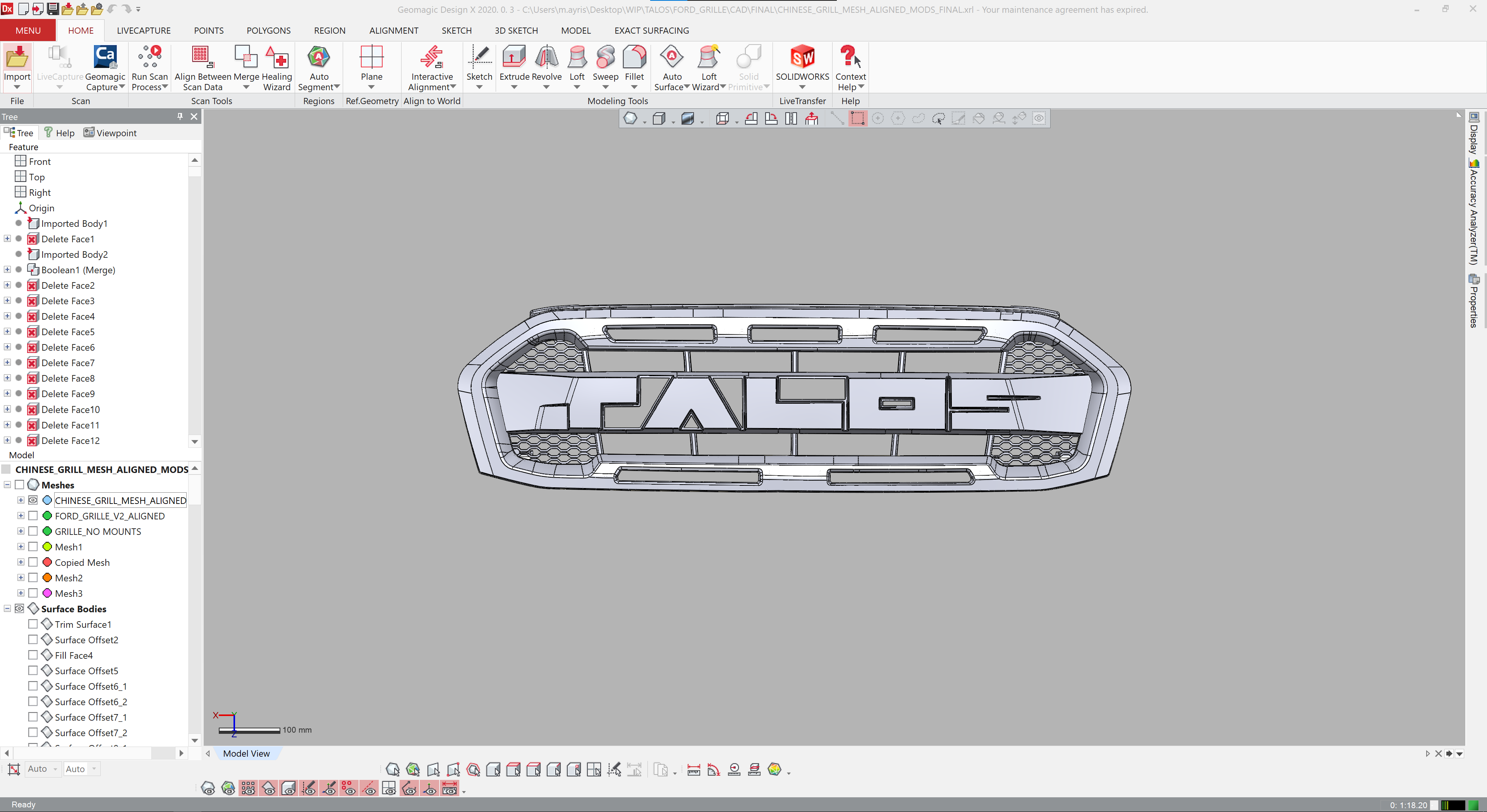
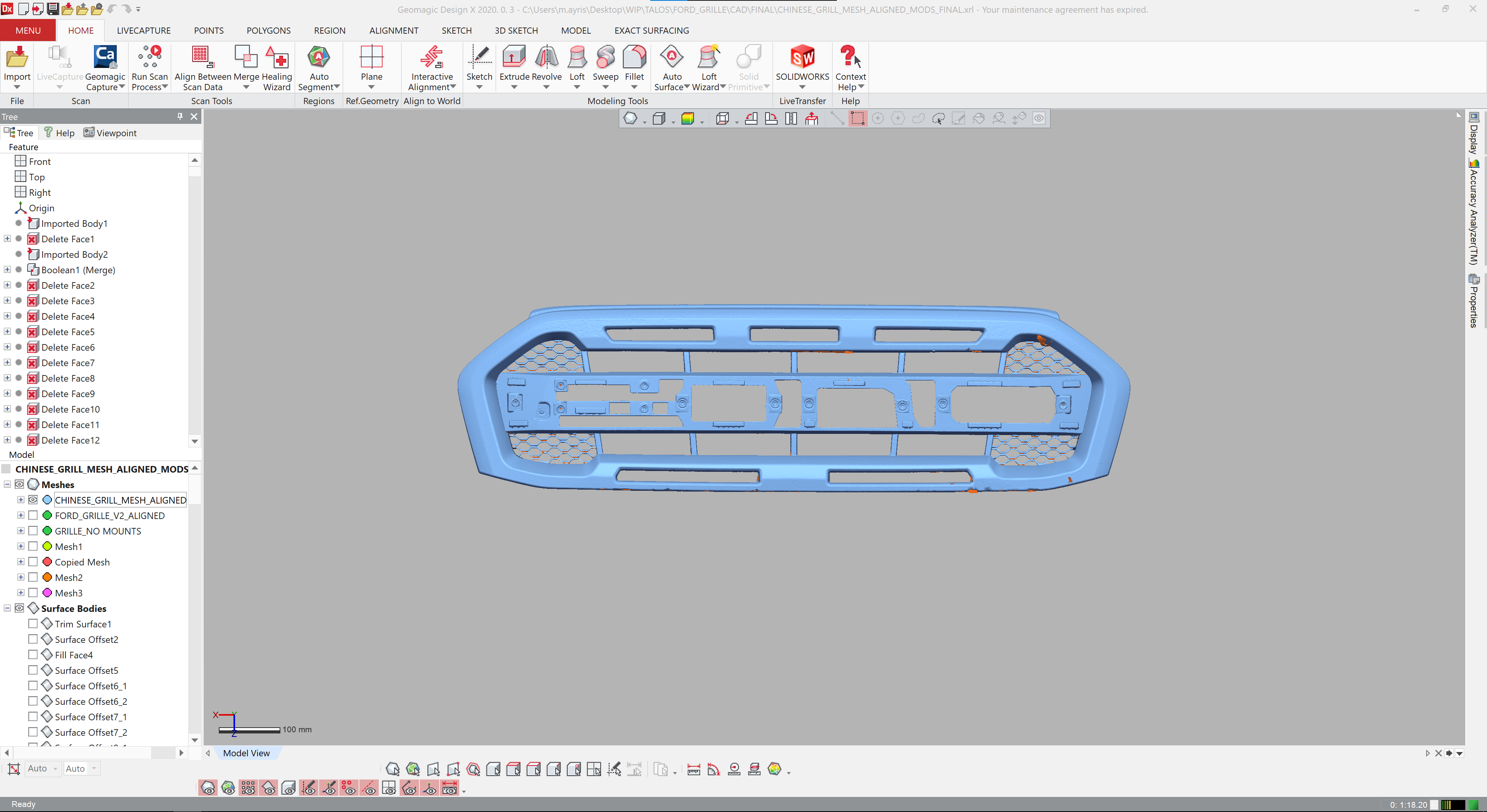
Cost Breakdown.
Project One. | ||
Product Details | Qty | Price |
Laser Scanning Laser scan existing Ford grille and truck to ensure accurate fit and function. |
2 | £500 |
Create STL File Data processing and alignment |
2 | £100 |
Reverse Engineer Parametrically reverse engineer grille to design intent. Add required modifications. |
1 | £1,400 |
Total | £2,000 ex VAT |
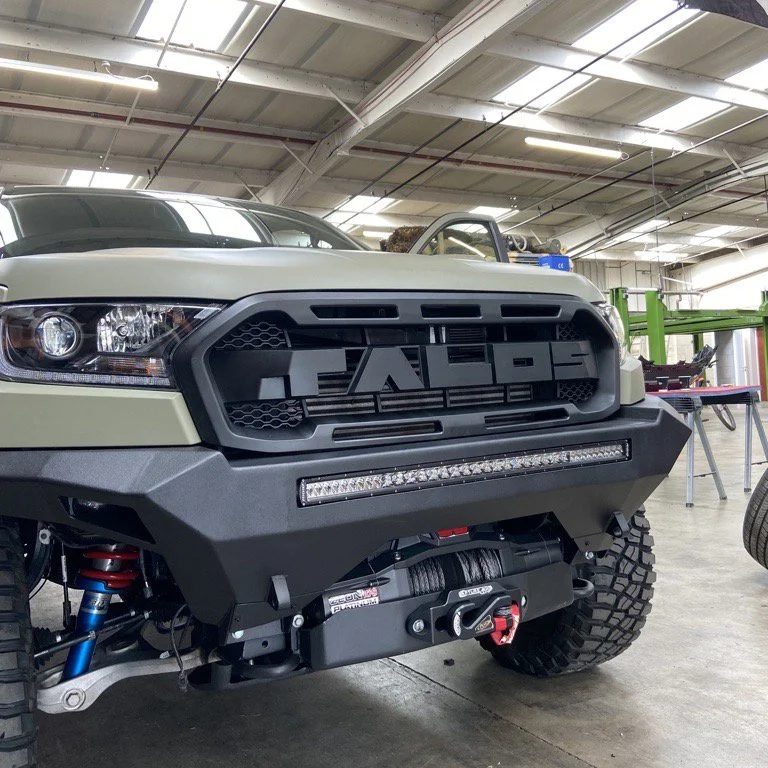
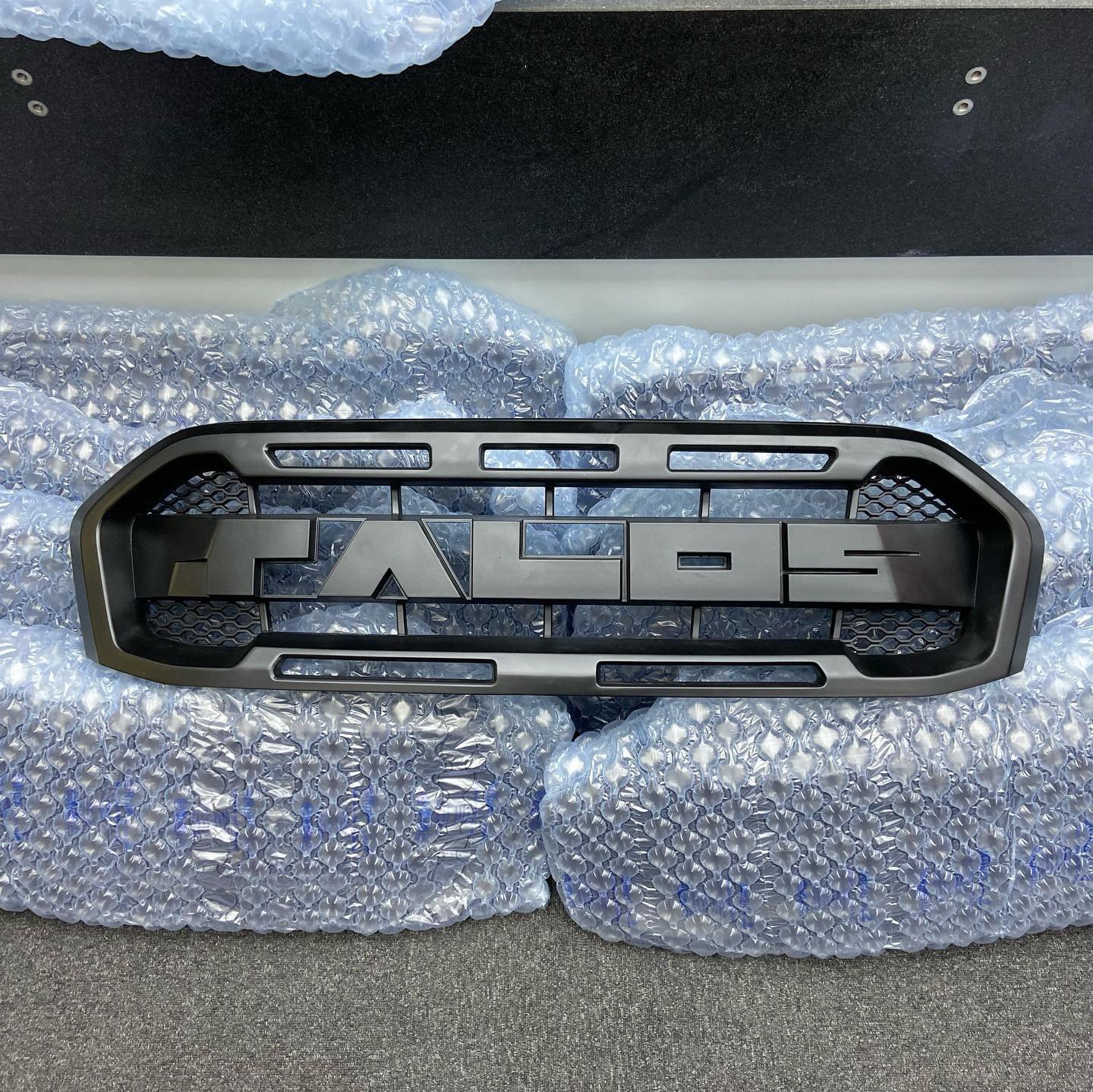

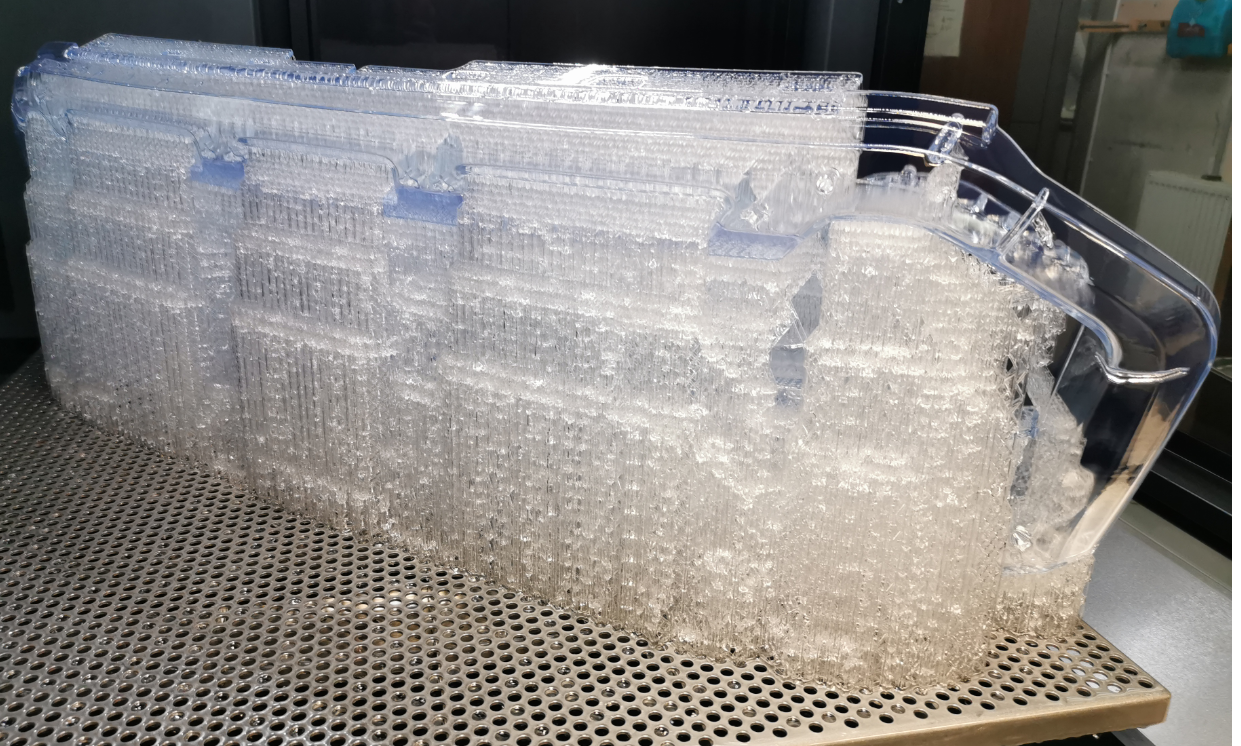
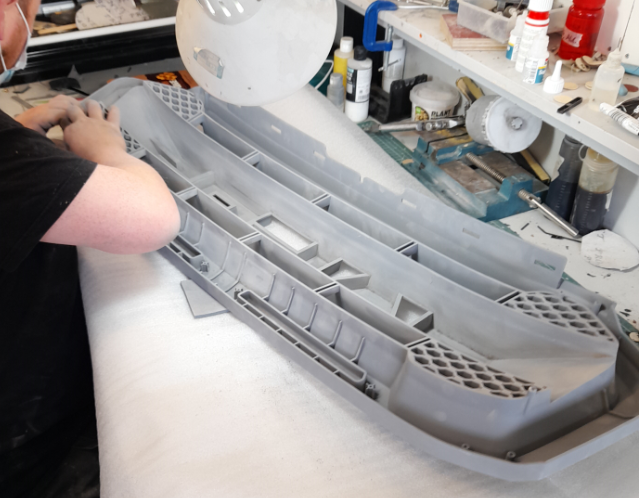